मुद्रण प्रौद्योगिकी के निरंतर विकास के साथ, कई प्रसिद्ध मुद्रण ब्रांडों के उपकरणों का प्रदर्शन न केवल बेहतर और बेहतर हो गया है, बल्कि स्वचालन की डिग्री में भी लगातार सुधार हुआ है। स्याही रंग रिमोट कंट्रोल सिस्टम कई बुद्धिमान मुद्रण का "मानक विन्यास" बन गया है, जिससे मुद्रित उत्पादों के स्याही रंग का नियंत्रण सुविधाजनक और विश्वसनीय हो गया है। हालाँकि, वास्तविक मुद्रण प्रक्रिया में, मुद्रित उत्पादों के प्रत्येक बैच के लिए स्थिर स्याही रंग प्राप्त करना आसान नहीं है। स्याही के रंग में बड़े अंतर के कारण गुणवत्ता संबंधी समस्याएं अक्सर उत्पादन में सामने आती हैं, जिससे कंपनी को नुकसान होता है।
मुद्रण से पूर्व अनुभव के आधार पर पूर्व समायोजन का अच्छा कार्य करना आवश्यक है
सबसे पहले, प्रमाण के क्षेत्र के अनुसार प्रत्येक रंग समूह स्याही फव्वारे की स्याही की मात्रा को मोटे तौर पर समायोजित करेंमुद्रणथाली। इंक रिमोट कंट्रोल सिस्टम से सुसज्जित मशीन पर यह काम पूरा करना आसान है। इसके लिए 80 फीसदी से ज्यादा का अनुमान होना चाहिए. रंग में बड़े अंतर से बचने के लिए मुद्रण करते समय स्याही की मात्रा को बड़ी रेंज में समायोजित न करें।
दूसरे, उत्पादन प्रक्रिया शीट की आवश्यकताओं और उत्पाद की विशेषताओं के अनुसार, औपचारिक मुद्रण के दौरान जल्दी में होने से बचने के लिए फीडर, कागज संग्रह, स्याही प्रदर्शन, दबाव आकार और अन्य लिंक को पूर्व-समायोजित करें। उनमें से, यह सुनिश्चित करना सबसे महत्वपूर्ण है कि फीडर विश्वसनीय, निरंतर और स्थिर रूप से कागज खिला सके। अनुभवी ऑपरेटर पहले कागज के प्रारूप और मोटाई के अनुसार ब्लोइंग, सक्शन, प्रेशर फुट, प्रेशर स्प्रिंग, पेपर प्रेसिंग व्हील, साइड गेज, फ्रंट गेज इत्यादि को पूर्व-समायोजित करते हैं, विभिन्न घटकों के बीच आंदोलन समन्वय संबंध को सीधा करते हैं। सुनिश्चित करें कि फीडर सुचारू रूप से कागज भरता है, और फीडर के टकराने के कारण स्याही के विभिन्न रंगों से बचें। यह अनुशंसा की जाती है कि अनुभवी कर्मचारी फीडर को पूर्व-समायोजित कर सकते हैं।
इसके अलावा, इसकी मुद्रण क्षमता में सुधार करने और सामान्य मुद्रण सुनिश्चित करने के लिए उपयोग किए गए कागज की गुणवत्ता और मुद्रित उत्पाद की छवि और पाठ क्षेत्र के आकार के अनुसार स्याही की चिपचिपाहट, तरलता और सूखापन को पहले से ठीक से समायोजित किया जाना चाहिए। . रबर के कपड़े और प्रिंटिंग प्लेट पर कागज के बाल और स्याही की त्वचा को साफ करने के लिए बार-बार बंद होने के कारण स्याही का रंग असमान नहीं होना चाहिए। यदि मुद्रण के बीच में विभिन्न चिपकने वाले रिमूवर और स्याही तेल जोड़े जाते हैं, तो रंग विचलन निश्चित है।
संक्षेप में, मशीन शुरू करने से पहले पूर्व-समायोजन का अच्छा काम करने से औपचारिक मुद्रण के बाद विफलता को काफी कम किया जा सकता है, और कप्तान के पास स्याही के रंग पर ध्यान केंद्रित करने के लिए समय और ऊर्जा होगी।
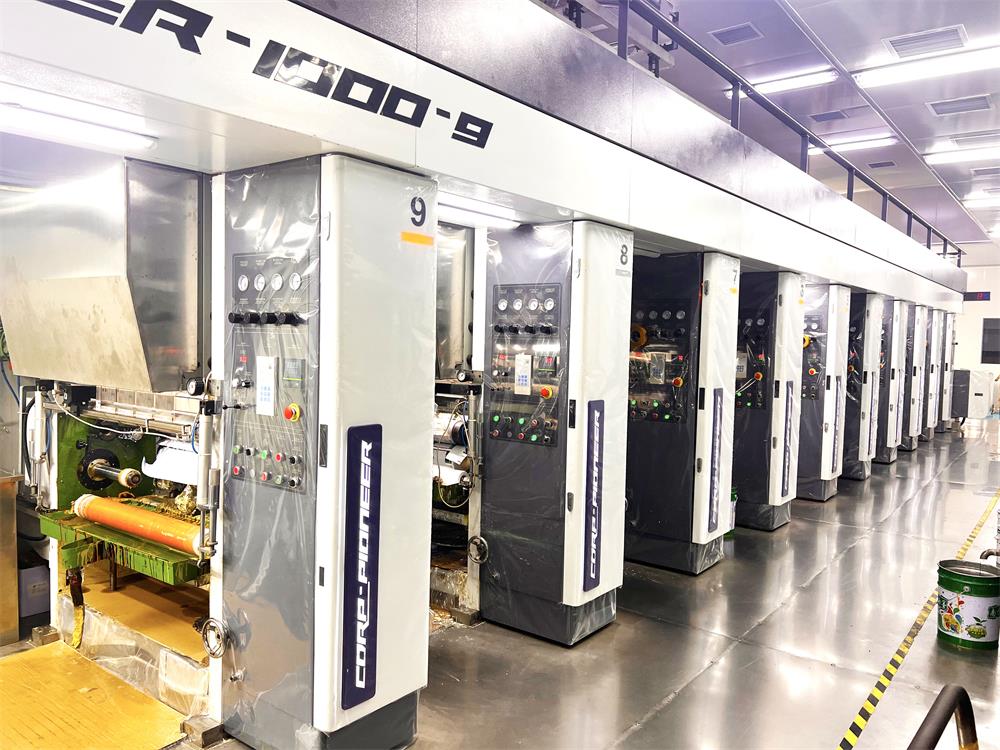
पानी और स्याही रोलर दबाव को सही ढंग से समायोजित करें
मुद्रण प्रक्रिया के दौरान, सुसंगत स्याही रंग के साथ एक प्रिंट प्राप्त करने के लिए प्रिंटिंग प्लेट की छवि और पाठ भाग को उचित मात्रा में स्याही के साथ लगातार और समान रूप से लागू किया जाना चाहिए। इसलिए, स्याही रोलर्स और स्याही रोलर्स, साथ ही स्याही रोलर्स और प्रिंटिंग प्लेट को अच्छा स्याही हस्तांतरण प्राप्त करने के लिए उचित संपर्क और रोलिंग संबंध बनाए रखना चाहिए। यदि यह कार्य सावधानीपूर्वक और सही ढंग से नहीं किया गया तो स्याही का रंग एक जैसा नहीं होगा। इसलिए, हर बार जब पानी और स्याही रोलर्स स्थापित किए जाते हैं, तो तनाव का परीक्षण करने के लिए फीलर गेज का उपयोग करने की पारंपरिक विधि के बजाय, उनके बीच दबाव को एक-एक करके समायोजित करने के लिए स्याही पट्टी को रोल करने की विधि का उपयोग किया जाता है, क्योंकि बाद में विभिन्न मानवीय कारकों के कारण एक बड़ी वास्तविक त्रुटि, और इसे बहु-रंग और उच्च गति वाली मशीनों पर प्रतिबंधित किया जाना चाहिए। जहां तक रोलिंग स्याही पट्टी की चौड़ाई का सवाल है, यह आम तौर पर 4 से 5 मिमी होना उपयुक्त है। पहले स्याही स्थानांतरण रोलर और स्याही स्ट्रिंग रोलर के बीच दबाव को समायोजित करें, फिर स्याही रोलर और स्याही स्ट्रिंग रोलर और प्रिंटिंग प्लेट सिलेंडर के बीच दबाव को समायोजित करें, और अंत में जल स्थानांतरण रोलर, प्लेट वॉटर रोलर के बीच दबाव को समायोजित करें। वॉटर स्ट्रिंग रोलर, और मध्यवर्ती रोलर, साथ ही प्लेट वॉटर रोलर और प्रिंटिंग प्लेट सिलेंडर के बीच दबाव। इन जलमार्गों के बीच स्याही की पट्टी 6 मिमी होनी चाहिए।
उपकरण को दो या तीन महीने के उपयोग के बाद पुन: समायोजित करने की आवश्यकता होती है, क्योंकि उच्च गति घर्षण की अवधि के बाद स्याही रोलर का व्यास छोटा हो जाएगा, खासकर ट्रांसमिशन में। स्याही रोलर्स के बीच दबाव कम हो जाता है, और जब स्याही रोलर्स उन पर जमा हो जाते हैं तो स्याही स्थानांतरित नहीं हो पाएगी। जब फीडर मुद्रण जारी रखने के लिए रुकता है या रुकता है, तो इस समय स्याही बड़ी होती है, जिससे पहले दर्जनों या सैकड़ों शीटों की स्याही का रंग गहरा हो जाता है, और आदर्श जल-स्याही संतुलन हासिल करना मुश्किल होता है। इस दोष को ढूंढना आम तौर पर आसान नहीं होता है, और यह महीन प्रिंट प्रिंट करते समय ही अधिक स्पष्ट होता है। संक्षेप में, इस संबंध में कार्रवाई सावधानीपूर्वक होनी चाहिए और विधि वैज्ञानिक होनी चाहिए, अन्यथा इससे पानी, स्याही पट्टी, प्रिंट के मुंह और पूंछ में स्याही की गहराई अलग-अलग हो जाएगी, कृत्रिम रूप से दोष पैदा होंगे और कठिनाई बढ़ जाएगी संचालन।
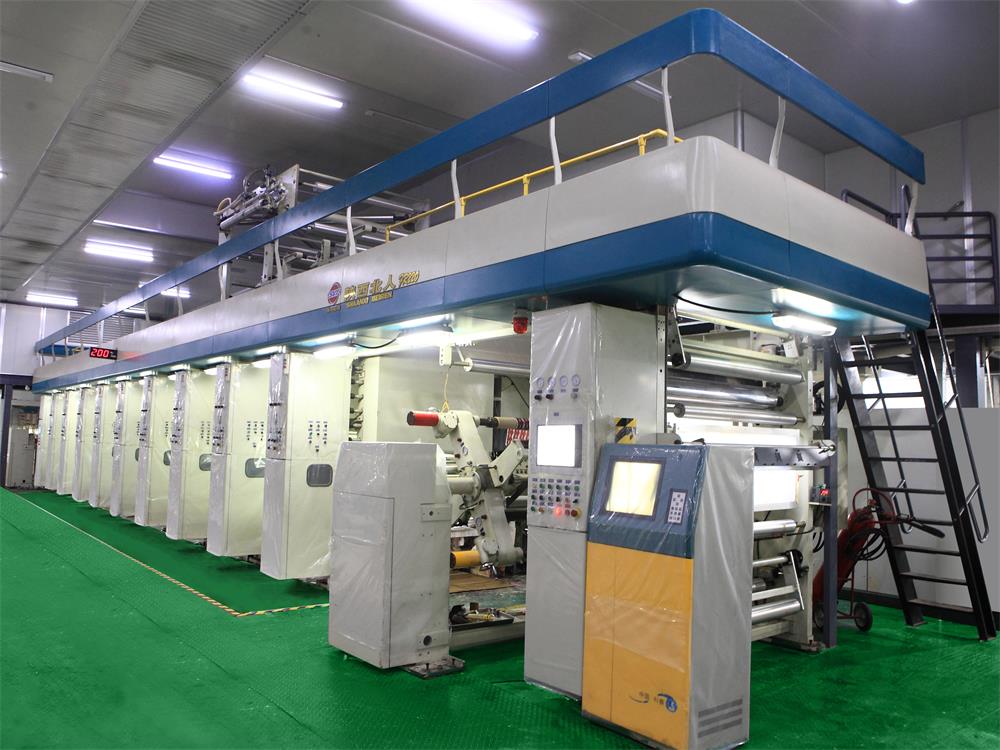
जल-स्याही संतुलन प्राप्त करना
जैसा कि हम सभी जानते हैं, जल-स्याही संतुलन ऑफसेट प्रिंटिंग का एक महत्वपूर्ण हिस्सा है। यदि पानी बड़ा है और स्याही बड़ी है, तो स्याही पानी-तेल में घुल जाएगी, और मुद्रित उत्पाद की गुणवत्ता निश्चित रूप से आदर्श नहीं होगी। दीर्घकालिक अभ्यास के माध्यम से, लेखक ने कुछ तकनीकों का पता लगाया है।
सबसे पहले, सुनिश्चित करें कि पानी और स्याही रोलर्स के बीच दबाव संबंध ठीक से समायोजित किया गया है, और फव्वारा समाधान और आइसोप्रोपिल अल्कोहल की सामग्री सामान्य मानकों को पूरा करती है। इस आधार पर, मशीन चालू करें, पानी और स्याही रोलर्स को बंद करें, और फिर प्रिंटिंग प्लेट की जांच करने के लिए मशीन को बंद करें। प्रिंटिंग प्लेट के किनारे पर हल्की 3 मिमी चिपचिपी गंदगी रहना सबसे अच्छा है। इस समय पानी की मात्रा को मुद्रण के लिए प्रारंभिक पानी की मात्रा के रूप में लेते हुए, सामान्य ग्राफिक उत्पादों की सामान्य छपाई की गारंटी दी जा सकती है, और पानी-स्याही संतुलन मूल रूप से प्राप्त किया जा सकता है।
दूसरे, पानी की मात्रा को अन्य कारकों के अनुसार लचीले ढंग से समायोजित किया जा सकता है, जैसे कि प्रिंटिंग प्लेट का बड़ा क्षेत्र, कागज की खुरदरी सतह, स्याही में एडिटिव्स जोड़ने की आवश्यकता, प्रिंटिंग की गति और परिवर्तन। हवा का तापमान और आर्द्रता।
इसके अलावा, लेखक ने यह भी पाया कि जब मशीन को प्रिंट करना शुरू किया जाता है, तो शरीर का तापमान कम होता है, और जब मशीन एक या दो घंटे तक तेज गति से चलती है, तो शरीर का तापमान, विशेष रूप से रबर रोलर का तापमान, कम हो जाता है। दोगुने से भी अधिक, या उससे भी अधिक की वृद्धि। इस समय, पानी की मात्रा धीरे-धीरे बढ़ाई जानी चाहिए जब तक कि पानी-स्याही एक नए संतुलन तक न पहुंच जाए।
यह देखा जा सकता है कि जल-स्याही संतुलन हासिल करना आसान नहीं है, और ऑपरेटर को इसे द्वंद्वात्मक रूप से तौलना और उपयोग करना पड़ता है। अन्यथा, स्याही के रंग की स्थिरता को नियंत्रित करना मुश्किल है, और उच्च गुणवत्ता वाले मुद्रित उत्पादों को मुद्रित नहीं किया जा सकता है।
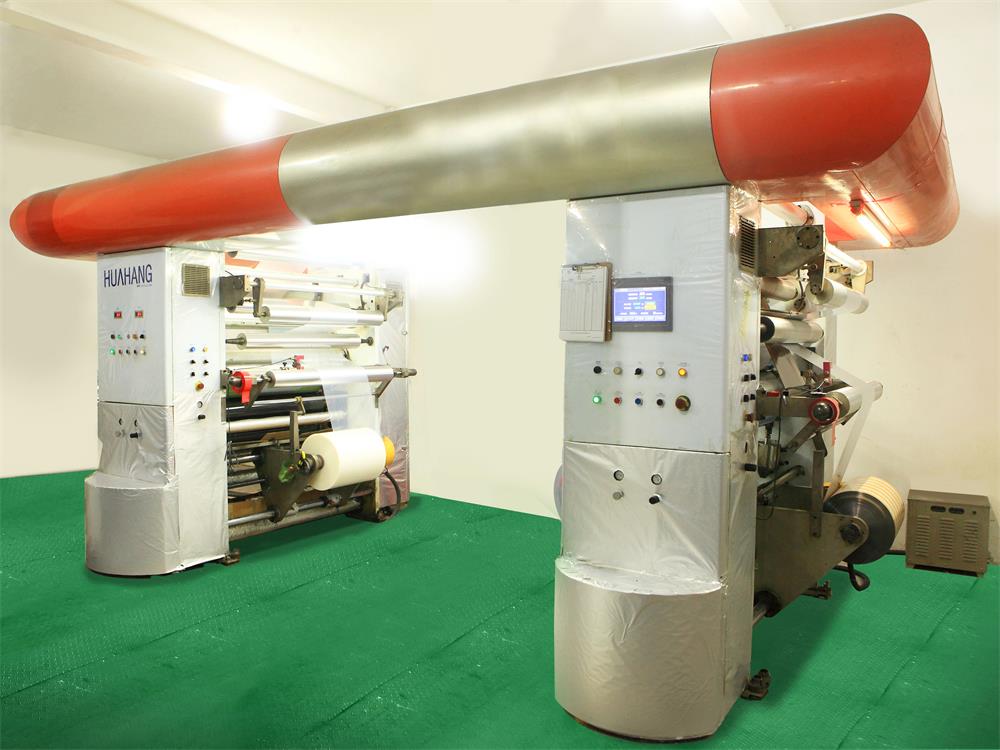
प्रूफ़रीडिंग और रंग अनुक्रम व्यवस्था
उत्पादन में, हमें अक्सर ऐसी स्थिति का सामना करना पड़ता है: ग्राहक द्वारा प्रदान किया गया नमूना बहुत गैर-मानक है, या बिना प्रूफ़िंग के केवल रंगीन इंकजेट ड्राफ्ट प्रदान किया जाता है। इस समय, हमें विशिष्ट स्थिति का विश्लेषण करने की आवश्यकता है, और हम प्रमाण के प्रभाव का पीछा करने के लिए स्याही की मात्रा को सख्ती से बढ़ाने या कम करने की विधि का उपयोग नहीं कर सकते हैं। भले ही यह शुरुआत में प्रमाण के करीब हो, स्याही के रंग की स्थिरता की गारंटी नहीं दी जा सकती है, और इस प्रकार मुद्रित उत्पाद की अंतिम गुणवत्ता की गारंटी नहीं दी जा सकती है। इस संबंध में, मुद्रण कारखाने को गंभीर और जिम्मेदार रवैये के साथ ग्राहक के साथ सक्रिय रूप से संवाद करना चाहिए, नमूने की समस्याओं और संशोधन सुझावों को इंगित करना चाहिए, और सहमति प्राप्त करने के बाद मुद्रण से पहले उचित समायोजन करना चाहिए।
उत्पादन में, बहु-रंगीन मशीन का मुद्रण रंग अनुक्रम आमतौर पर स्याही की चिपचिपाहट से निर्धारित होता है। चूँकि बहु-रंग मुद्रण में, स्याही को गीले-पर-गीले तरीके से लगाया जाता है, केवल सर्वोत्तम सुपरइम्पोज़िशन दर प्राप्त करके ही एक स्थिर और सुसंगत स्याही का रंग मुद्रित किया जा सकता है। मुद्रण रंग अनुक्रम की व्यवस्था मुद्रित उत्पाद की विशेषताओं और गुणवत्ता आवश्यकताओं के अनुरूप होनी चाहिए, और अपरिवर्तित नहीं रह सकती। साथ ही, स्याही की चिपचिपाहट को भी समायोजित किया जा सकता है। उदाहरण के लिए, एक बैंगनी कवर और एक आसमानी नीले कवर में अलग-अलग मुद्रण रंग अनुक्रम होते हैं: पहले के लिए सियान पहले और मैजेंटा दूसरे और बाद के लिए मैजेंटा पहले और सियान दूसरे। अन्यथा, अधिक मुद्रित रंग धब्बेदार हो जाएंगे, जो न तो चिकने होंगे और न ही स्थिर होंगे। उदाहरण के लिए, एक प्रिंट के लिए जो मुख्य रूप से काला है, काले को यथासंभव अंतिम रंग समूह में रखा जाना चाहिए। इस तरह, काले रंग की चमक बेहतर होती है और मशीन के अंदर खरोंच और रंग मिश्रण से बचा जाता है।
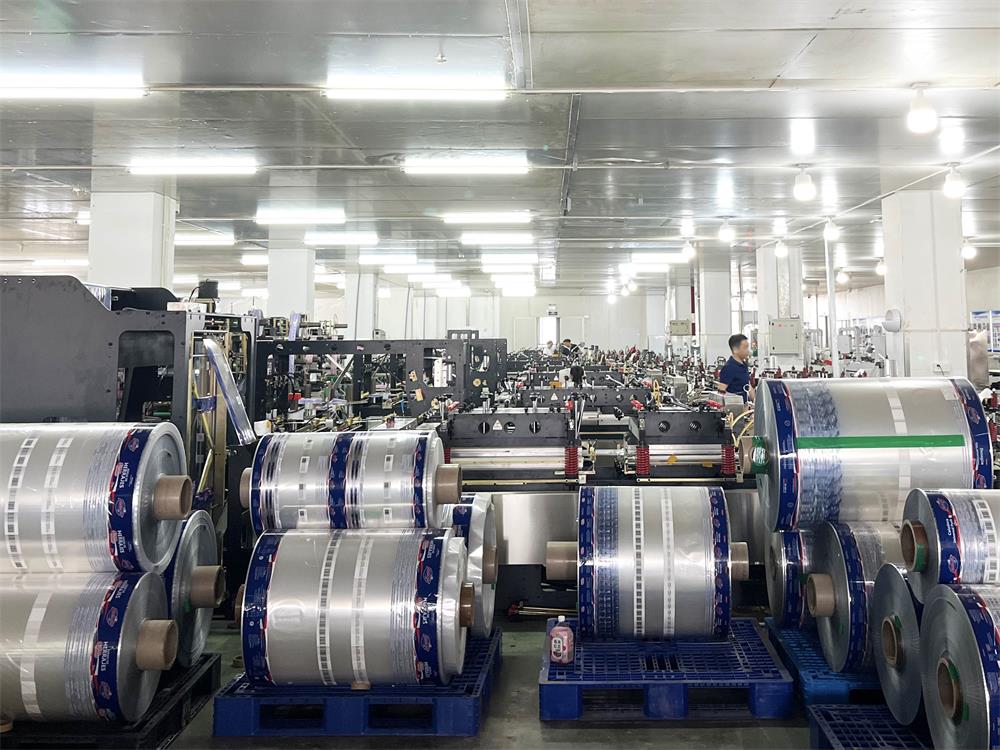
अच्छी परिचालन आदतें विकसित करें और कार्य उत्तरदायित्व को मजबूत करें
कोई भी कार्य करते समय हमारे अंदर जिम्मेदारी की उच्च भावना और गुणवत्ता की प्रबल भावना होनी चाहिए। हमें प्रक्रिया संचालन को मानकीकृत करना चाहिए और "तीन स्तरों" और "तीन परिश्रम" जैसी अच्छी पारंपरिक आदतों का पालन करना चाहिए। उदाहरण के तौर पर नमूनों की लगातार तुलना को लें। नमूने पर हस्ताक्षर नमूने की तुलना करते समय, दूरी, कोण, प्रकाश स्रोत आदि में अंतर के कारण, दृश्य पक्षपाती होगा, जिसके परिणामस्वरूप स्याही का रंग असंगत होगा। इस समय, हस्ताक्षर का नमूना हटा दिया जाना चाहिए और सावधानीपूर्वक तुलना की जानी चाहिए; प्लेट परिवर्तन के कारण स्याही के रंग विचलन को कम करने के लिए लंबे समय तक चलने वाली प्रिंटिंग प्लेट को बेक करने की आवश्यकता होती है; रबर के कपड़े को बार-बार साफ करना चाहिए, और स्याही के रंग को स्थिर बनाने के लिए प्रत्येक सफाई के बाद अधिक ब्लॉटिंग पेपर रखना चाहिए; फीडर रुकने के बाद, जो पाँच या छह शीट अभी-अभी छपी हैं वे बहुत गहरे रंग की हैं और उन्हें बाहर निकालने की आवश्यकता है। मुद्रण की गति बहुत तेज़ नहीं होनी चाहिए. महत्वपूर्ण बात यह है कि मशीन को स्थिर और सामान्य रखा जाए; स्याही के फव्वारे में स्याही जोड़ते समय, क्योंकि नई स्याही सख्त होती है और उसमें तरलता कम होती है, स्याही की मात्रा को प्रभावित करने और स्याही के रंग में विचलन से बचने के लिए इसे कई बार हिलाया जाना चाहिए।
ऑपरेटरों को सावधानीपूर्वक सीखना, निरीक्षण करना और विश्लेषण करना जारी रखना चाहिए, सभी पहलुओं से स्याही के रंग में परिवर्तन को प्रभावित करने वाले कारकों का पता लगाना चाहिए, और उन्हें ठीक से रोकने और दूर करने के लिए संबंधित उपाय करने चाहिए, स्याही के रंग की स्थिरता और स्थिरता में सुधार करने का प्रयास करना चाहिए मुद्रित उत्पाद, और मुद्रित उत्पादों की गुणवत्ता में प्रभावी ढंग से सुधार करते हैं।
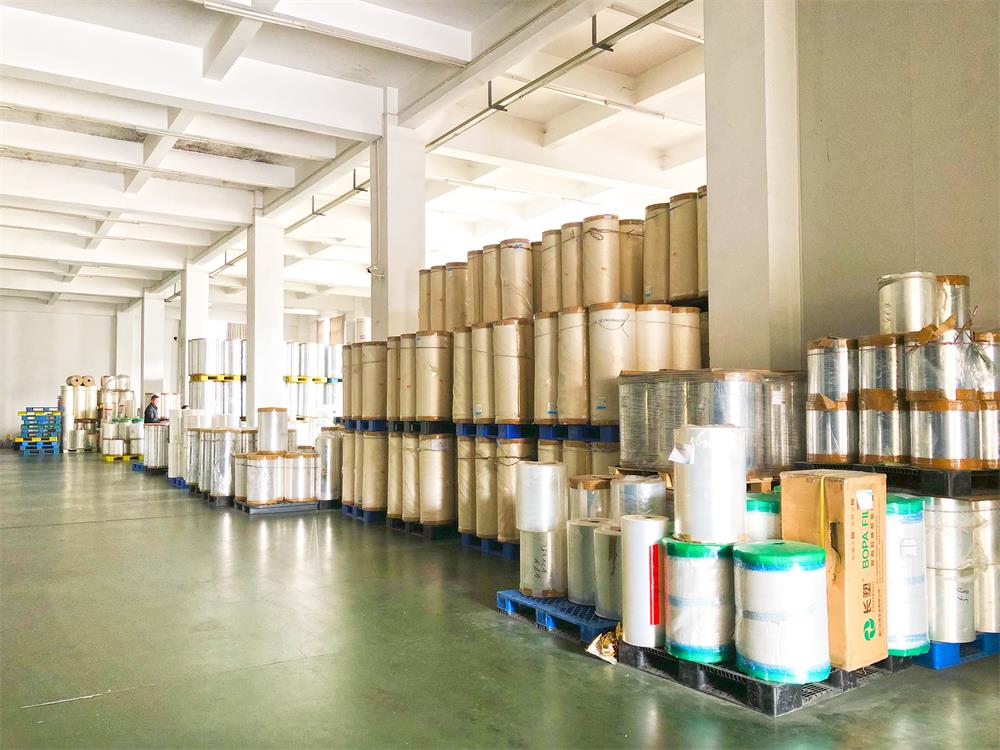
पोस्ट समय: मई-27-2024